On November 25, 2014, Parker Hannifin , a global leader in the field of motion and control , exhibited at the 2014 China International Construction Machinery, Building Materials Machinery, Engineering Vehicles and Equipment Expo (bauma China 2014), and for the first time released several innovations in the Chinese market. Energy-efficient, high-efficiency new products showcase Parker Hannifin's technological leadership in drive and control, hydraulics and filtration.
Kurt Keller, President of Parker Hannibal Asia Pacific, stated: “Efficient production and energy saving and emission reduction are the arduous challenges facing the entire construction machinery industry. Parker Hannifin always adheres to technological innovation and continuous change to solve problems in improving energy efficiency and protecting the environment. In addition, we also use the company's winning strategy as the core to help our customers improve their return on investment and achieve profitable growth."
Parker Hannibal 2014 BMW Exhibition Media Meet
“Pike Hannifin is one of the first three foreign joint ventures established since China opened up its foreign direct investment abroad. It has been deepening China for more than 30 years and has made considerable progress under the huge lifting of China’s construction machinery market.â€, Huang Jincheng, President of Parker Hanniq Greater China, said, “With the transformation and upgrading of the industry and the pace of Chinese companies seeking internationalization, Parker Hanniou has always been committed to the technology and R&D capabilities, overall solutions and the most Quality services are provided to Chinese customers and work with Chinese companies to promote the healthy, efficient and sustainable development of China's construction machinery industry."
Parker Hannifin’s main innovative energy-saving products and technologies at the 2014 BMW Shanghai show include:
Parker Hannifin's newly developed IMV intelligent flow control system uses an integrated valve block to perform independent inlet and outlet throttling control of the actuator, minimizing the energy loss of the hydraulic system and greatly improving the energy utilization efficiency. After testing, the use of this system can reduce fuel consumption by up to 20% for the host and increase production efficiency by 5%.
Parker Hannibal 2014 BMW Exhibition Booth
The design of the Intellinder Absolute Position Sensor combines well-established optics with an independently developed lens, providing excellent resolution and repeatability, providing condition monitoring, detecting potential cylinder failures, and preventing them from affecting operation. It can be easily integrated into the cylinder without the need for exposed sensors or complicated wiring, making it an ideal solution for severe outdoor engineering environments.
Parker Hannifin EHP electronic hydraulic pumps have a complete solution that can be applied to a large voltage range to fit different battery packs. Fast and convenient product selection and general product design make it a wide range of applications. Product performance is high efficiency, stable and quiet operation, can reduce the size of the power system.
The new EO-3® connection system makes installation simpler, more efficient and safer. The new threading technology enables the installation of EO-3® to be simpler and faster than the current connection technology; the visualization of its installation results enables all users to directly observe whether the installation is in place, thus ensuring the safety and reliability of the device.
In recent years, Parker Hannifin has completed a series of major investments in China, building automation plants in Wuxi, hydraulic system plants and filtration system plants in Shanghai, continuously expanding its product portfolio in China, and expanding R&D and technical teams. Improve customer service levels to meet Chinese customers' demand for high value-added products and services, confirming their commitment to the long-term development and continued investment in the Chinese market.
Parker Hannifin currently has 19 production bases and 7 regional offices in China, more than 2,000 product lines, products cover more than 50 markets, providing aerospace, environmental control, electromechanical, filtration, fluid and gas processing for enterprises. , Hydraulic, pneumatic, process control, sealed nine major technical solutions and services. Product applications and solutions mainly involve diesel engines, wind power, shipbuilding, marine exploration, iron and steel, large construction machinery, high-speed railways, and factory automation.
Stamping Parts:
The processing method for stamping and forging are plastic processing (or pressure processing), forging stamping blank collectively. Is hot-rolled and cold-rolled steel sheet and strip. The world of steel, 60 ~ 70% is the plate, mostly made by stamping products. Automobile body, chassis, tank, radiator, boiler drum, vessel shell, electric machine, electric iron core silicon steel sheet are stamping processing. Instruments, household appliances, bicycles, office machinery, household utensils and other products, there are a large number of Stamping Parts stamping. Is powered by conventional or special punching equipment, make sheet metal in the mold directly affected by the deformation force and deformation, thus A certain shape, size and performance of the product parts production technology. The sheet metal, mold and equipment are the three elements of stamping. Temperature divided by stamping hot stamping and cold stamping. The former is suitable for high deformation resistance, sheet metal plasticity is poor; the latter was carried out at room temperature, is commonly used in stamping method the sheet metal plastic processing. It is (or pressure processing) one of the main methods, but also forming part of materials engineering. Stamping mold called stamping die, or die. The die is the material (metal or non-metal) batch processing into the special tool stamping. Die is of vital importance in the in the press, did not meet the requirements of the die, it is difficult to carry out production batch stamping die; no advanced, advanced stamping process can not be achieved. The stamping process and die, stamping equipment and stamping materials to constitute three stamping processing Only when they combine with each other can they get the stamping parts.
WHY Stamping:
Stamping parts and castings, forgings, a thin, uniform, light, strong character. Stamping can be produced from other methods is difficult to manufacture with stiffeners, stamping parts stamping rib, rolling or burring of the workpiece, to improve its rigidity. Because of the use of precision molds, workpiece precision, and high repetition accuracy, specifications, can punch a hole nest, boss. Cold stamping generally no longer cutting machining, or only a small amount of cutting. The hot stamping precision and surface state below the cold stamping, but still better than the casting, forging, machining less.
(1) Stamping processing is of high production efficiency, convenient operation, easy to realize mechanization and automation. This is because the stamping dies and stamping equipment rely on to complete the processing, ordinary press trips per minute up to dozens of times, high pressure per minute up to hundreds or even thousands of times, and each press stroke you may get a red piece.
(2) The stamping die ensure the dimension and shape precision stamping parts, and generally do not damage the surface quality of stamping, and die life is generally longer, so the stamping quality, good interchangeability, "as like as two peas" feature.
(3) Stamping can press the processing size range is large, complex shape parts, such as a small clock stopwatch, large car rails, covering parts, stamping and material hardening effect of cold deformation, punching strength and stiffness are higher..
(4) Stamping generally without cutting scrap generated, material consumption is less, and no other heating equipment, which is a kind of material saving, energy saving and processing, lower the cost of stamping parts.
Category:
Stamping is mainly according to the process of classification, can be divided into separation process and the forming process of two categories. The separation process also known as blanking, its purpose is to make the stamping parts along the contour line must be separated from the sheet, and guarantee the quality of the separation section (Table 1). The forming process is designed to make sheet metal in broken slab under the condition of plastic deformation, the workpiece into the required shape and size. In the actual production, often a variety of integrated process applied to a workpiece. The blanking, bending, shear, tensile, bulging, spinning, correction is the main stamping process of several.
Mainly speaking,based on the three different material,we can make steel stamping farts,copper alloy stamping parts and aluminium alloy stamping parts.
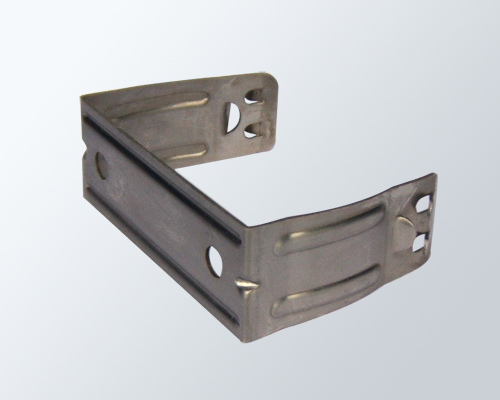
Stamping Parts
Stamping Parts,Steel Stamping,Copper Stamping,Aluminium Stamping
VESTA Motoring Ltd , http://www.vesta-industry.com