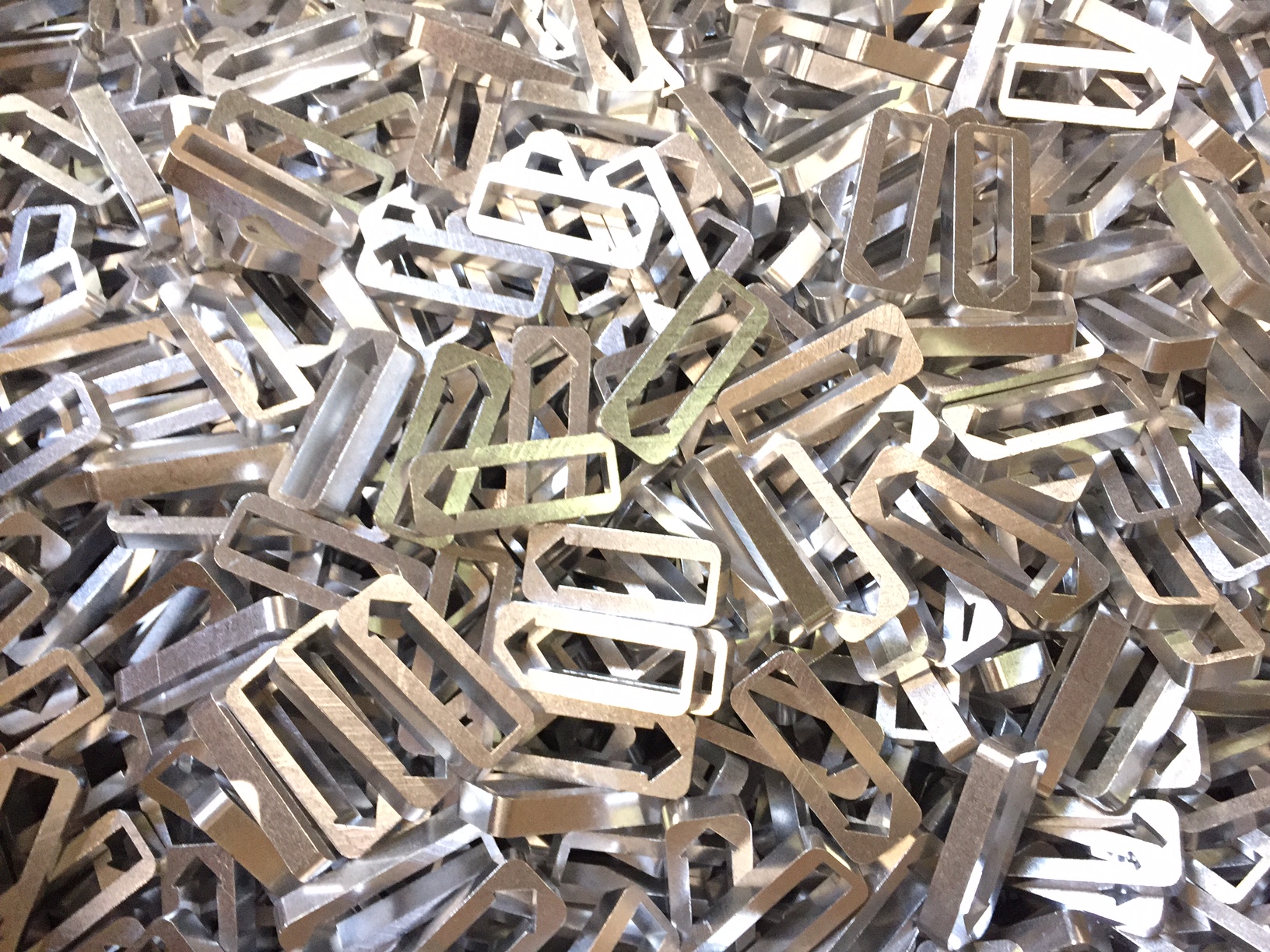
Benefits of Vibratory Finishing
Updated: December 22, 2023Vibratory finishing is a widely used technique in the manufacturing sector that helps achieve high-quality surface finishes for small components and parts. This process is known for its efficiency, speed, and ability to deliver consistent results across large volumes of products. Whether you're looking to clean, deburr, or polish, vibratory finishing offers a reliable solution tailored for industrial applications.
With various types of systems available—such as spiral bowl finishers and long radius vibratory machines—manufacturers can choose the best option based on their specific needs. These systems are designed not only for performance but also for cost-effectiveness and ease of use, making them ideal for mass production environments where time and quality are critical.
What Is the Vibratory Finishing Process?
The vibratory finishing process involves placing a large number of parts into a bowl or tub that vibrates at a controlled frequency. As the parts move within the bowl, they come into contact with an abrasive media, which gradually removes burrs, impurities, and rough edges. This friction-based method ensures that each part receives a uniform finish without damaging delicate surfaces.
Whether you opt for wet or dry vibratory finishing, the process can be adapted to suit different materials and requirements. The wet process, for instance, uses water to enhance cleaning and can be more environmentally friendly when recycled properly. This flexibility makes vibratory finishing a popular choice across industries like automotive, medical, and consumer goods.
Why Choose Vibratory Finishing Services?
Manufacturers who invest in vibratory finishing services often experience multiple benefits, including:
- Cost-Effective: Vibratory finishing allows for the efficient processing of large batches, reducing labor and equipment costs. It’s an economical alternative to other finishing methods that may require more time and resources.
- Low Maintenance: These machines are built to last and require minimal upkeep, ensuring continuous operation and fewer interruptions. This reliability translates to higher productivity and lower long-term costs.
- Versatile Application: From metals like stainless steel, aluminum, and copper to plastics and ceramics, vibratory finishing works with a wide range of materials. Machines can also be customized to meet specific project requirements.
- Fragile Material Friendly: Despite the high level of friction involved, vibratory finishing is gentle enough to handle delicate components without causing damage. This makes it ideal for precision parts that require a smooth, polished finish.
Explore Our Finishing Solutions
At Finishing Systems, we offer a comprehensive range of vibratory finishing solutions designed to meet the needs of diverse industries. Whether you're working with medical devices, automotive components, or consumer products, our advanced systems ensure a fast, clean, and precise finish every time.
Our machines are equipped with cutting-edge technology to maximize efficiency and reduce downtime. If you’re looking for a reliable partner in finishing processes, we’re here to help. Contact us today to learn more about our services and how we can support your manufacturing goals.
Contact Us Today
Jiangsu Bailite Transmission Technology Co., Ltd , https://www.zsindustrialbelt.com