In order to improve the processing efficiency during roughing and finishing, the tool with larger diameter is generally used for machining. Therefore, there is a large margin in the roughing after machining. The local shape of the part is not milled when finishing. Use partial milling. Because the cutting is smooth at the same level, the cutting can be smooth, and the spiral, broken line, S-line or fixed-point pre-drilling method can be used between the layers. Therefore, the two tool paths are most commonly used during programming. It is also two ideal rough milling tool paths.
After the tool path is generated, the correctness of the program can be checked by 3D dynamic simulation, and the entire machining process can be visually observed. The tool location data file is generated after the determination is made correctly. The tool location data file is the data and information of the part machining tool path generated by the CAM software. The tool position data file generated by CAM cannot drive the CNC machine tool. It must process the tool position data file according to the system selection of the machine tool or edit the post-processing file to generate the NC file that matches the machine tool.
Programs generated by automatic programming generally have a very large amount of information, and it is impossible to input them manually. Usually, a method in which a PC and a machine tool communicate directly is used. There are two methods of transmission. The first one is to input the program into the machine memory through the communication interface, and the machine tool is transferred into the program in the memory for processing. The second method is to process the PC and the machine tool while using the transmission. It can be seen that to become an excellent CNC programmer, you must be familiar with the operation performance of various machine tools, master manual programming, part processing technology, material properties of parts and cutting amount of various tools, etc., and must be able to use CAD/CAM with ease. software. (Finish)
Steel Pipe Roll Forming Machine
High Frequency Welding Tube Mill
Our High Frequency Welding Tube Mill is intended for manufacturing of round pipe of Φ16mm-Φ127mm with thickness of 0.5 mm–5.0 mm from cold-rolled and hot-rolled coil strip by means of unclosed tubular blank with its subsequent welding into tube, edge heating by means of solid state high-frequency welder, longitudinal seam welding in rolls of tube welding machine, cooling, further sizing or shaping and on-stream cutting of endless tube in measured lengths.
Finished product can be of round, square or rectangular pipes.
Pipe diameter: Ø16–Ø127mm
Pipe Thickness: 0.5– 5.0mm
Pipe Length: 6-9m
Length Tolerance: 0-3mm
Material: Low Carbon steel (δb≤500Mpa, δs≤235Mpa)
Inner diameter: Φ580-Φ610mm
Outer diameter: Φ900-1500mmStrip steel thickness: 0.5mm-5.0mm
The maximum weight: 5.0 tons
Dynamic power: AC380V±10%, 3phases, 50Hz±10%
Control Power: AC220V±10%, one phase, 50Hz ±10%
Electric installed capacity: appro 450KW
Reservoir for High Frequency equipment:15 m³, one set
Reservoir for circulating cooling water:15 m³, one set
f) High Frequency Welding Tube Mill Compressed air:
Pressure: 0.4Mpa
Flow: 0.5m3/h
g) High Frequency Welding Tube Mill speed:
30-90m/min
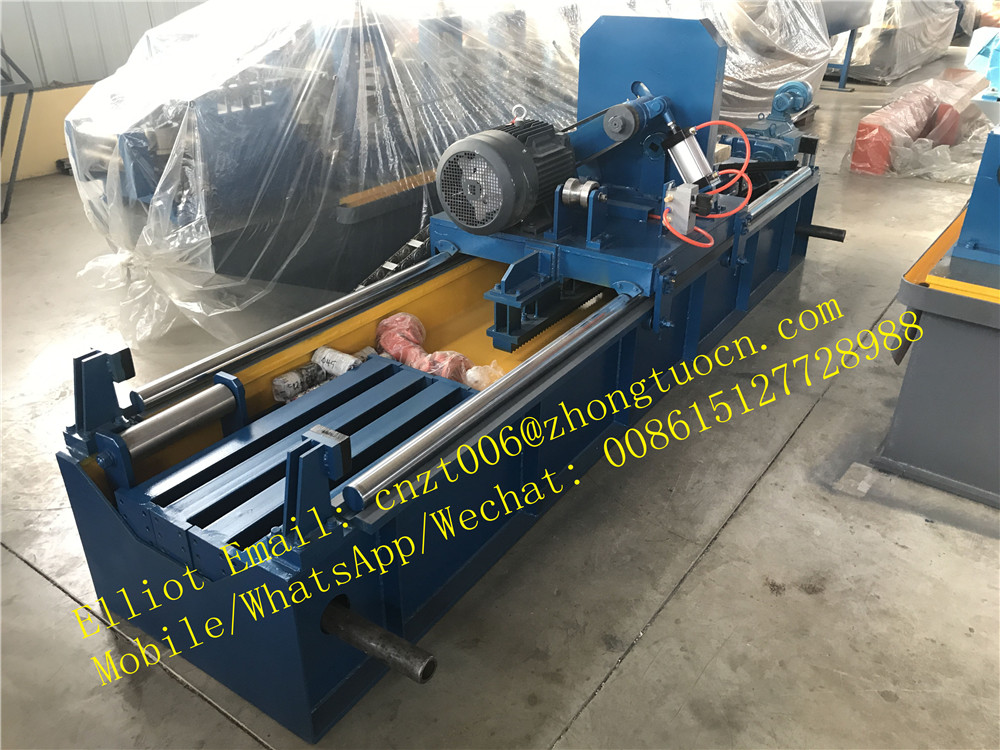
Why choose to cooperate with us ?
1. We are professional manufacturer, so we can offer better price and after-sale service and shorter delivery time.
2. We have strong design & technical ability, we can design and manufacture as customer's requirement.
3. Our factory has been approved ISO 9001 certificate.
4. We have much experience for installation and training experience overseas.
5. We have successfully exported our machines to more than 90 countries, We all get good feedback.
6. We provide a free two years warranty for all our items.
7. OEM brand.
1.How to get a quotation of tube rolling line ?
Give me the diameters and thickness for the pipe .
Other spicific requirements is welcome, such as the speed,power and voltage you want.
2. Terms of payment ?
30% T/T, Balance to be paid before shipping after inspection.Also we accept the payment L/C, O/A , D/P.
3. What is your after-sale service ?
High Frequency Welding Tube Mill warranty period is 24 months, if the broken parts can't be repaired, we can send new to replace for free, but you need to pay the express cost yourself. we supply the technical support for the whole life of the equipment.
4. How to visit your factory ?
a.Fly to Beijing airport: By high speed train From Beijing Nan to Cangzhou Xi (1 hour), then we can pick up you.b.Fly to Shanghai Airport: By high speed train From Shanghai Hongqiao to Cangzhou Xi(4.5 hours), then we can pick up you.
Steel Pipe Roll Forming Machine,Carbon Steel Pipe Making Machine, High Frequency Welding Pipe Making Machine,Steel Pipe Making Machine
Zhongtuo Roll Forming Machinery Co., ltd , https://www.frameforming.nl